Where money meets mission
Featured Articles
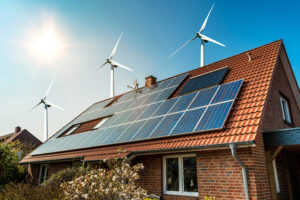
Energy-Efficient Mortgages: Everything You Need to Know (2022)
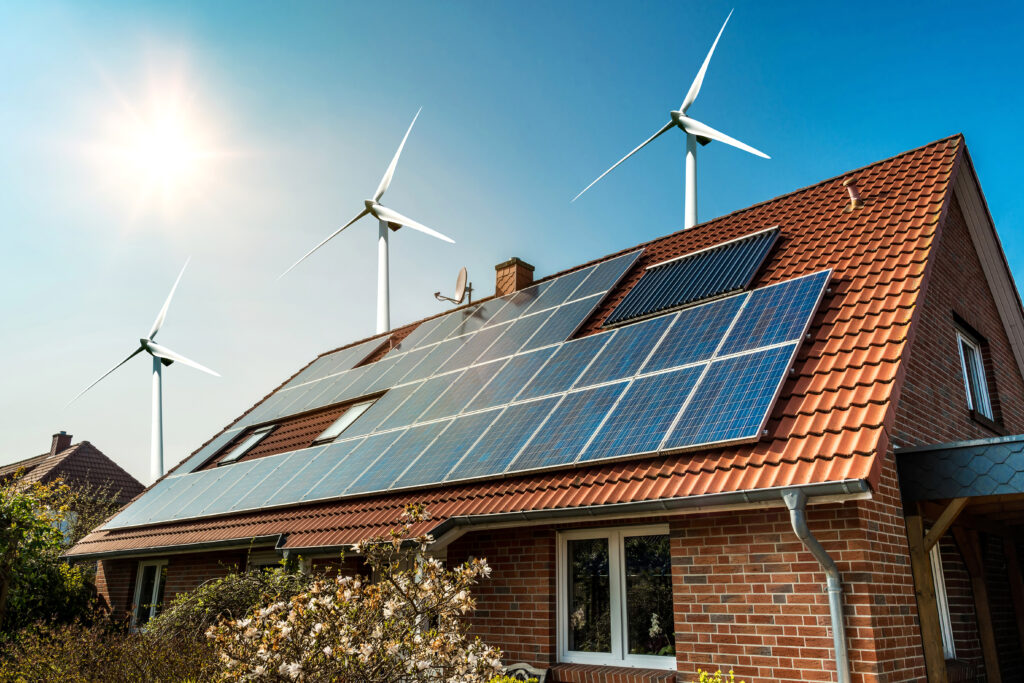
What Is an Energy-Efficient Mortgage?
So, what are green mortgages? Also called energy-efficient mortgages or eco mortgages, green mortgages serve two primary purposes:- They give home buyers the capital they need to make efficiency-boosting changes to their existing or future homes for more sustainable living.
- They help current buyers qualify for loans to purchase homes that are already energy-efficient.
- Katie and Laura purchased their home five years ago. They’re ready to refinance and renovate their current home since interest rates have decreased since the loan closed. While they apply for refinancing, they can also express an interest in an energy-efficient mortgage—a loan program that will fund the eco-friendly changes they want to make, like replacing their home’s old insulation.
- Angie and Pat are scouring the market for their first home. But they’re having difficulty qualifying for a mortgage that will secure the energy-efficient home they’re interested in. It features solar panels, upgraded insulation, and a new HVAC system. They could pursue an energy-efficient mortgage to give them the extra capital they need to qualify for the slightly larger mortgage needed to buy the eco-friendly property.
Examples of Common Energy-Efficient Mortgage Projects
Depending on how much funding you secure, you can get involved in any of the following projects :- Invest in green energy by installing solar panels or adding wind turbines to their property or roof
- Decrease your home’s energy use by updating the HVAC system, adding a radiant barrier to the attic space, and replacing their insulation with higher R-value products
- Replace tank water heaters with tankless products
- Remove single-pane windows and install double- or triple-pane products
- Add a water reclamation technology to their plumbing system
- Replace appliances with low-energy, low-flow, upgraded ones
How to Qualify for an Energy-Efficient Mortgage
So, you think an energy-efficient mortgage loan could meet your financial needs and help make your home more efficient—what’s next? Let’s explore how to become approved for an eco-mortgage.#1 Purchase a New Home
You can qualify for a green mortgage in one of two ways—by purchasing a new home or refinancing the mortgage loan on your current home. When purchasing a new home, it’s important to note how an energy-efficient mortgage fits into the loan structuring process:- Your primary mortgage loan will cover the majority of the cost of your new home.
- Any energy-efficient mortgage products you pursue during the home-buying process can help you:
- Pay for the energy-efficient upgrades you want to make, or
- Put down enough to qualify for a primary mortgage loan on an energy-efficient property.
#2 Refinance the Mortgage on Your Current Home
If you want to take out an energy-efficient mortgage to decrease your current home’s footprint, you can do so by refinancing your mortgage loan. Becoming approved for refinancing is usually the same as the approval process for a traditional loan. Depending on your lender, the process may include the following steps:- The loan servicer and underwriters will review your creditworthiness by examining:
- Income documents
- Tax returns
- Employment history
- Credit information
- Next, the servicer will approve a loan for a specific amount.
- Finally, you’ll close on the loan by signing documents and paying a down payment and a variety of fees, like:
- Title search fees
- Loan origination fees
- Other closing costs
Types of Energy Efficient Mortgages
There are three types of energy-efficient mortgages available as of 2022—conventional loans, Federal Housing Administration (FHA) loans, and Veterans Affairs (VA) loans. Let’s break down each type in more detail.#1 Conventional Energy-Efficient Mortgages
Current or future home buyers can secure a conventional energy-efficient mortgage from various loan servicers—including the companies providing mortgage pre-approval. Conventional loans are regulated via one of two programs:- Fannie Mae’s HomeStyle Energy mortgage program
- Freddie Mac’s GreenCHOICE mortgage program
#2 FHA Energy-Efficient Mortgage
The Federal Housing Administration (FHA) offers low-cost, insured mortgage loans and energy-efficient mortgages to both home purchasers and refinancers. To qualify, applicants for an FHA green mortgage must:- Secure approval for a primary mortgage loan from the FHA
- Prove the cost-effectiveness of their intended improvements
- Complete a home energy assessment to optimize the efficiency of projects funded
- The cost estimate derived from the home energy assessment
- 5% of the:
- Adjusted value
- 115% of the median area home price
- 150% of the national conforming mortgage limit
#3 VA Energy-Efficient Mortgage
If you have a history of current or past military employment, service, or time spent in reserve, you may qualify for a VA energy-efficient mortgage. The US Department of Veterans Affairs (the VA) offers both:- Home purchasing mortgages
- Home refinance mortgages
- Be based upon documented improvement costs (for loans up to $3,000)
- Not produce monthly loan payments more costly than future reduced energy costs (for loans up to $6,000)
- Correspond with a home value determination completed by the VA (for loans over $6,000)
Benefits of Energy-Efficient Mortgages
If you’re considering using an energy-efficient mortgage to afford a more eco-friendly home, it can help to weigh the pros and cons before deciding. Green loans offer a variety of benefits for current or future homeowners:- Interest rates are low – Lenders typically provide low interest rates if you pursue a conventional, FHA, or VA energy-efficient loan. They can because their investment is protected by the energy efficiency improvements, you’ll complete once you receive the funds.
- You can borrow more than the property is worth – With both purchase and refinance loans, eco-mortgages can increase your loan size—even if the property isn’t currently worth the loan amount you need.
- Overall cost savings – Energy-efficient loans can help you decrease your home energy costs, potentially leading to long-term savings. In addition, when you fund eco-friendly home upgrades with an energy-efficient mortgage, you’re likely choosing the lowest-interest financing option available for home improvements.
Drawbacks of Energy-Efficient Mortgages
Even if the benefits interest you, energy-efficient mortgages might not be right for every homebuyer or refinancer. Consider the following possible drawbacks before signing on the dotted line:- Interest could cancel out savings – While interest rates are generally low for green mortgages, monthly interest payments could still cancel out your monthly energy savings until you’ve completely paid off your mortgage. Calculate your interest and predicted savings carefully before you close.
- Efficiency upgrades can vary widely in cost – Unless you complete a home energy assessment beforehand, it can be difficult to determine how much money you’ll spend on energy-efficient upgrades. Try to develop as clear a picture as possible of your upgrade costs before requesting a loan amount.
- You may face additional red tape – Especially if you apply for an FHA or VA loan, you might need to complete additional procedures or have to provide extra documentation to apply for a green mortgage.
Is an Energy-Efficient Mortgage Right for You?
So, should you pursue a green mortgage? The answer may be different for everyone. But if any of the following circumstances apply to you, an energy-efficient mortgage could be worth pursuing. You might want a green mortgage if you’re a current homeowner and one or more of the following is true:- You’re saving some money each month
- Interest rates are generally lower than they were when you bought your home
- You plan to stay in your current home for the next year
- You want to purchase the most efficient home possible
- You’re willing to invest time and money to improve your home’s efficiency
Aspiration: Green Money Management And More
The climate finance movement has mobilized multiple sectors to reduce emissions. Green mortgages can help you secure or create your dream energy-efficient home. But, they’re not the only environmentally responsible financial product on the market today. Enter Aspiration—the money management solution that prioritizes you and the planet. Unlike traditional financial institutions, we never use your hard-earned deposits to finance non-renewable energy projects. Instead, our sustainable financial services fund the innovators of the future, developing the green tech that will reverse climate change for good. Plus, we can help you reduce your carbon footprint with a green credit card with built-in carbon offsetting, a sustainable investment fund, and so much more. When you’re ready to use your wallet for good, Aspiration is here to help.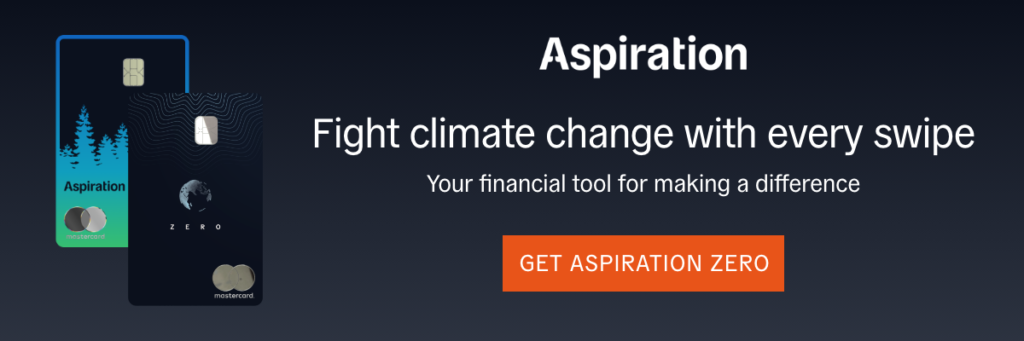
Make Change Staff
September 3, 2022
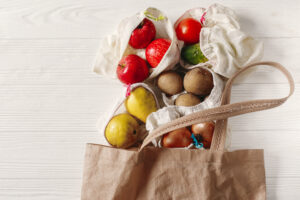
10 Examples of Sustainable Living You Can Start Doing Today
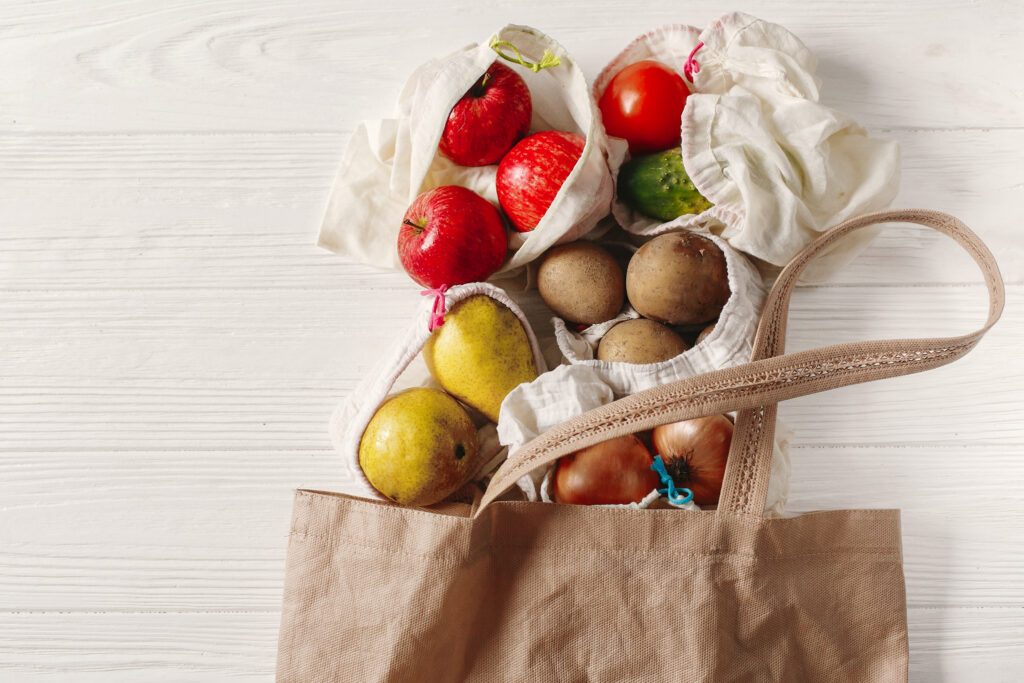
#1 Making Your Voice Heard
While even small lifestyle changes can create positive effects on the planet, climate change reversal can’t happen without massive-scale action by powerful institutions. To contribute to change at scale in your everyday life, you can make your voice heard by:- Placing regular calls or sending emails to your federal, state, and local representatives. You can find contact information for your representatives at USAGov.
- Voting and volunteering for candidates committed to climate action. You can look up your local candidates and learn about their stances on websites like Ballotpedia.
- Participating in direct actions that lead to institutional pressure. You can find resources on climate advocacy groups on websites like the US Climate Action Network (USCAN).
#2 Phasing Out Single-Use Plastic
Single-use plastics account for 40% of the plastic produced yearly. These include plastic bags, food wrappers, bottled water containers, and others that don't degrade for years. While you contribute to systemic change-making, you can advance the cause of sustainability at home by phasing out your use of single-use plastic items. Reducing your plastic use can have all kinds of positive effects for the planet—from reducing waste to conserving energy and resources. Eliminate plastic bags and bring a reusable tote to stores to lessen plastic waste. Add the following reusable items to your home to decrease your reliance on disposable plastic products:- Reusable water bottles made from metal, durable plastic, and glass
- Cloth grocery bags
- Glass or heavy-duty plastic leftovers containers
- Metal, silicone, or glass straws
#3 Turning Your Lawn into a Pollinator Paradise
While you may admire the look and feel of a lush, green lawn, maintaining perfectly-manicured grass simply isn’t sustainable. Each year, Americans use 3 trillion gallons of water, 200 million gallons of fuel, and 70 million pounds of pesticide products to maintain their lawns alone. Instead of wasting time, resources, and money on a lawn, you can make your green space more sustainable by:- Replacing grass with low-maintenance, organic alternatives like pebbles, pine straw, or mulch
- Introducing pollinator plants native to your ecosystem
- Completely replacing your grass with clover or wildflowers
#4 Reducing Your Household Energy Use
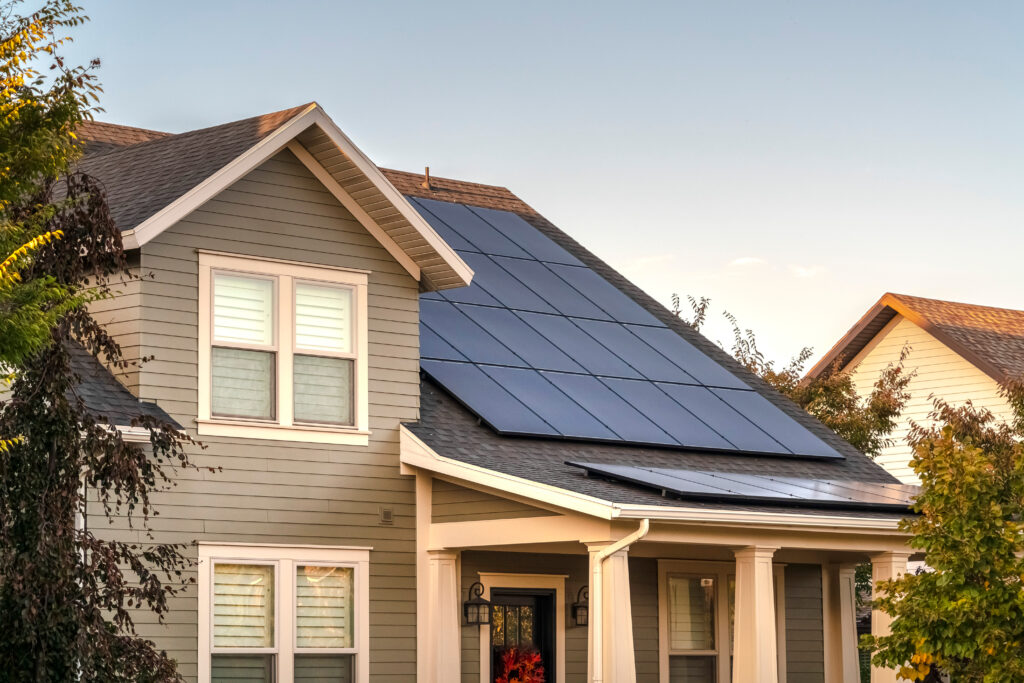
- Changing the way you wash and dry clothes by using cold/cool water cycles to reduce water-heating energy use and opting for a clothesline instead of the dryer when the weather permits
- Taking shorter, cooler showers
- Unplugging appliances and devices when they’re not in use
#5 Using Reclaimed Water
Reclaimed water can be a powerful resource. In industrial applications, it can be used to extend water resources for everything from agriculture to environmental restoration. But you can also reclaim water to live more sustainably at home. In general, reclaimed water is safe to use for:- Watering plants
- Washing your car
- Bathing your pets
#6 Composting to Reduce Waste
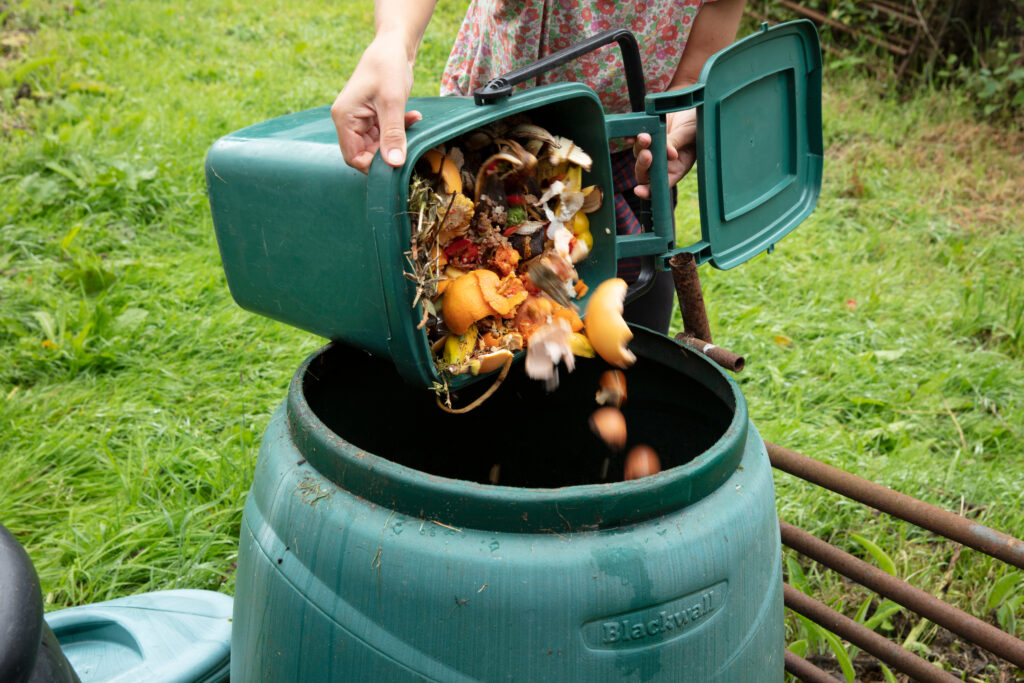
- Browns – Outdoor waste like branches and dead leaves
- Greens – Organic food products like vegetable peels, fruit scraps, and coffee grounds
- Water – Water helps your compost operation decompose at a healthy rate
#7 Rethinking Your Commute
You might be using more energy during your commute than you think. On average, people in the U.S. contribute 3.2 tonnes of CO2 per year just from their daily drive to and from work. Millions of greenhouse gas emissions are released into our atmosphere, leading to air pollution due to fossil fuel and other pollutants. Instead of hopping in the car and riding by yourself to the office, consider more sustainable transportation methods like:- Starting or joining a carpool with coworkers or neighbors
- Hitching a ride on public transit
- Biking, scootering, or skateboarding to work
#8 Shopping Conscientiously
There are many ways to live more sustainably through your wallet. One of these sustainable practices is purchasing goods and services from companies that do right by the environment. Here’s how to shop sustainably:- Make a list of the brands you use most often.
- Eliminate brands that create a negative environmental impact.
- Replace them with companies putting in the work for the planet.
- Shop at zero waste and Bring Your Own Container stores (BYOC).
- Buy only what you need and use all of it to lessen food waste.
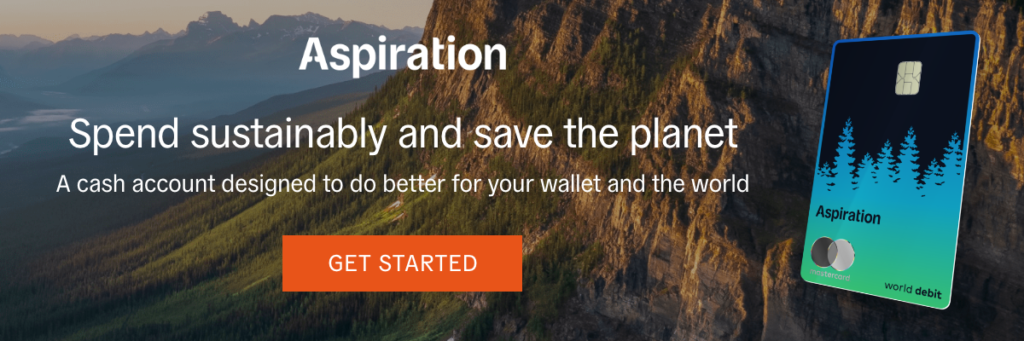
#9 Avoiding Fast Fashion
Living a sustainable lifestyle means saying goodbye to fast fashion. According to the UN Environment Programme, the fashion industry accounts for up to 10% of global carbon dioxide output and air pollution—a more significant carbon footprint than international flights and shipping combined. The U.S. throws away up to 11.3 million tons of textile yearly. We all love the ability to find affordable, accessible clothing. But fast fashion brands can contribute to irresponsible energy use and encourage a wasteful mindset. This is because low-quality, cheap goods often aren’t sustainably produced and need to be quickly replaced. Instead of opting for cheaply-made, low-price clothes, shoes, and accessories, you can decrease your waste and save money by spending a little more on a product that will last.#10 Thrifting
Speaking of long-lasting goods, plenty of them end up at thrift stores. This makes your local resale shop an excellent place to pick up high-quality, affordable products with life left in them. Thrift stores have nearly everything these days:- Appliances
- Furniture
- Clothes
- Shoes
- Cookware
- Home decor
- Storage solutions (like baskets and clothes hangers)
Aspiration: Where You Can Fight Climate Change with Your Wallet
Did you know that your financial institution might be funding fossil fuels projects? In 2021 alone, the world‘s biggest financial services providers (including American institutions like Wells Fargo and Chase) provided $742 billion in financing to the fossil fuel industry. If you’re looking for a simple way to incorporate sustainable practices and live green, consider switching to a sustainable financial services provider. Start living a sustainable life today. Aspiration offers numerous money management solutions to help consumers contribute to the green economy, tackle their carbon footprints, and invest in climate change reversal. When you switch to sustainable financial services, you can make a simple, personal change that contributes to climate action at scale. Sources: Climate Science. Does Personal Action Matter?. https://climatescience.org/advanced-personal-action National Geographic. The world's plastic pollution crisis explained. https://www.nationalgeographic.com/environment/article/plastic-pollution AlmostZeroWaste. Why Should We Reduce The Use Of Plastic. https://www.almostzerowaste.com/reduce-plastic-waste/ Energy.Gov. Reducing Electricity Use and Costs. https://www.energy.gov/energysaver/reducing-electricity-use-and-costs US Environmental Protection Agency. Basic Information about Water Reuse. https://www.epa.gov/waterreuse/basic-information-about-water-reuse Natural Resources Defense Fund. More Sustainable (and Beautiful) Alternatives to a Grass Lawn. https://www.nrdc.org/stories/more-sustainable-and-beautiful-alternatives-grass-lawn US Environmental Protection Agency. Composting at Home. https://www.epa.gov/recycle/composting-home Buffer. Is Remote Work Greener? We Calculated Buffer’s Carbon Footprint to Find Out. https://buffer.com/resources/carbon-footprint Bloomberg. The Global Glut of Clothing Is an Environmental Crisis. https://www.bloomberg.com/graphics/2022-fashion-industry-environmental-impact/ Investopedia. Fast Fashion. https://www.investopedia.com/terms/f/fast-fashion.asp Reuters. World’s Top Banks Pumped $742 Bln into Fossil Fuels in 2021 – Report. https://www.reuters.com/business/sustainable-business/worlds-top-banks-pumped-742-bln-into-fossil-fuels-2021-report-2022-03-30/Make Change Staff
September 2, 2022
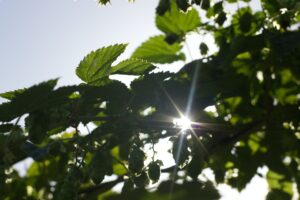
7 Reasons Why Sustainable Living is Important
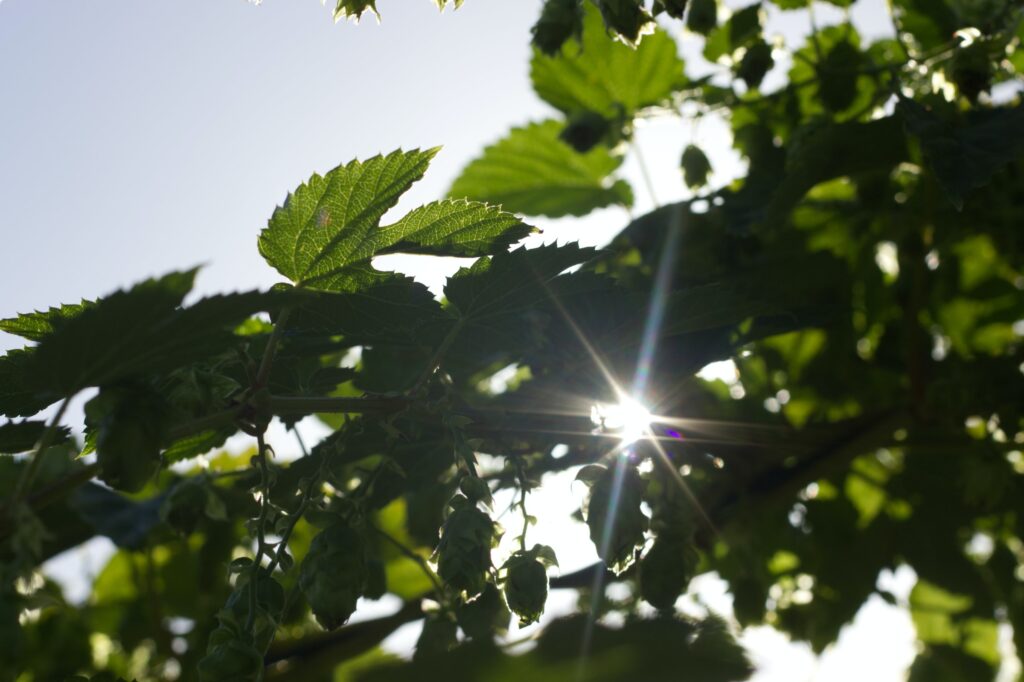
#1 Repairing the Environment is Time Sensitive
If you watch the news, you might know that rising global temperatures have already contributed to a rise in dangerous weather events like heat waves, heavy rains, floods, droughts, and cyclones. These extreme weather events, in turn, can lead to environmental damage, economic loss, and even human death. According to the United States Environmental Protection Agency, climate change has caused heat waves to occur more frequently in major cities across the United States. In addition, the agency also reported the threats to health and well-being as it affects every facet of life—food, air, water, and shelter. However, we can still turn things around by adopting an environmental sustainability mindset to lower greenhouse gas emissions. Here’s the hopeful news:- We can stabilize temperatures by shifting to net-zero carbon emissions by 2050.
- There’s reason to believe we can make that goal if we halve global emissions by 2030.
- Climate scientists say that we have the necessary technology in multiple industries to make that 2030 goal happen.
#2 Sustainable Living Can Create Real Change
When facing a challenge as daunting as climate change, believing that our cumulative actions can make a difference can be difficult. That’s why it’s important to remember that we have already faced a major environmental crisis in our atmosphere—and won. In the 1980s, scientists discovered that Chlorofluorocarbons or CFCs, a greenhouse gas (chemicals once common in refrigerators and air conditioners), were destroying the ozone layer. The world responded by banning CFCs. Today, not only has the ozone layer nearly healed, but a recent study suggests the ban on CFCs actually helped fight global warming by a few degrees. Even if you might not see the impact immediately, making the products we use every day more environmentally friendly can have a real and dramatic effect on the environment.#3 Changes in Your Personal Life Can Contribute to Bigger Change
Some people have argued that since most emissions come from major corporations, encouraging individuals to live sustainably doesn’t matter. The evidence we have suggests the exact opposite. When people focus on living sustainably in their own lives, it can encourage others to live sustainably. That, in turn, can increase the odds of corporations and governments making environmentally-friendly changes on a structural level. Living a more sustainable life not only limits your own carbon footprint, but it can also help contribute to the kind of major industry and government changes that we need.The Push for Sustainable Product Packaging
Stateside and worldwide, the zero waste movement is gaining steam, and large and small businesses are responding. According to a study by McKinsey & Company, 55% of U.S. consumers described themselves as highly concerned or very concerned about the environmental impact of product packaging. By insisting on more sustainable product packaging, consumers drive the growth of social sustainability from individuals to a larger scope. Positive change starts in a sustainable home and by adopting practices that create zero waste, minimal food waste, and decreased reliance on fossil fuel.#4 Sustainable Lifestyle Choices Can Improve Your Physical Health
You might already associate sustainable living with a healthier Earth. But some of the recommended ways to lower your carbon footprint can also make you healthier. For example, consider the positive impact of these sustainable practices:- Using walking and bicycling as a form of transportation – Walking or biking instead of driving can help reduce carbon emissions. At the same time, both walking and biking can help you maintain a healthy weight and strengthen your muscles.
- Choosing a more plant-based diet – Shifting to a plant-based diet can help fight global warming by reducing the emissions created by animal farming. It could also improve your health. Studies suggest plant-focused diets can reduce the risk of heart disease, diabetes, certain cancers, and depression.
#5 Sustainable Products Can Save You Money
You may be used to how your current comforts and resource usage impact your wallet. But sometimes, going green could help the planet and save you money. So how does going green save money? Well, it can be as small as changing a lightbulb to a more efficient one. On average, you could save about $1,560 in utilities and natural gas over the next fifty years by:- Using LED light bulbs
- Unplugging devices when they’re not in use
- Lowering the heat during the winter
- Using less air conditioning during the summer
- Using cold water for your dishwasher and washing machine
- Using reusable containers instead of single-use plastics
- Purchasing more energy-efficient appliances
#6 Actions Like Planting Trees Can Reduce Carbon in Our Atmosphere
Because trees absorb carbon dioxide, scientists have proposed planting trees as a way to neutralize some of the carbon emissions that contribute to global warming. While planting trees alone can’t completely offset global warming, reforestation offers a simple, effective way to reduce carbon emissions. If combined with a strategy to reduce fossil fuels, planting trees can be a crucial part of a well-rounded plan to live sustainably and eventually halt global climate change.#7 The Way You Spend Money Can Make a Difference
Every year, major financial institutions make hundreds of billions of dollars from their customers. They often turn around and invest that money in extreme oil drilling and pipeline projects that hurt our environment. But now, clean finance companies are making it possible to make smart money decisions and help protect the environment. By changing how you manage your money, you could make a difference toward a more sustainable future with every cent you spend. For more guidance, check out our tips on how to shop sustainably.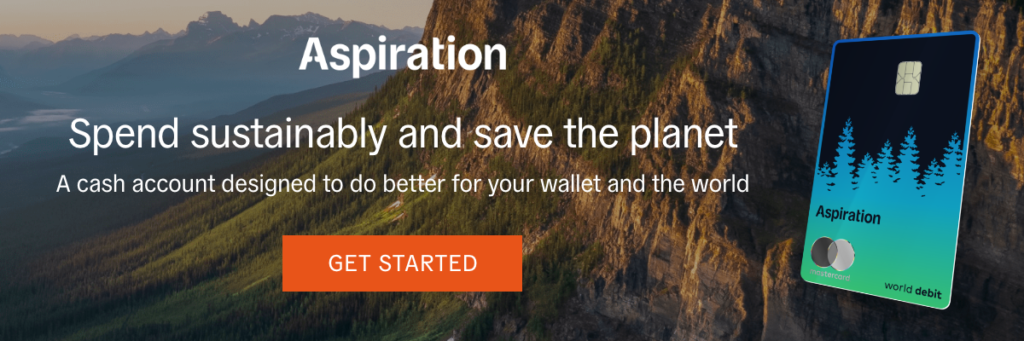
Live Sustainably and Get Cash Back with Aspiration
As you’ve seen, sustainable living can make a substantial, positive difference for our planet and all who live here. Fortunately, there are many easy ways to start living sustainably today. At Aspiration, we promise your deposits won’t fund fossil fuel projects. Plus, we offer up to 10% cash back on purchases through our Conscience Coalition program. We think living sustainably is more important than ever. But the good news is that there are plenty of accessible, effective ways you can make a difference. For more on sustainable living, discover simple examples of sustainable living you can implement in your own lifestyle today. Sources: BBC. Plant-based diet can fight climate change - UN. https://www.bbc.com/news/science-environment-49238749 CNBC. Here are 8 easy ways to save money by going green. https://www.cnbc.com/2021/06/26/here-are-8-easy-ways-to-save-money-by-going-green.html CNN. A 1980s ban on CFCs to heal the ozone layer is also shaving degrees off global warming, study says. https://www.cnn.com/2021/08/19/world/cfcs-ozone-montreal-protocol-climate-study-intl-scn/index.html EPA. Climate Change Indicators: Weather and Climate. https://www.epa.gov/climate-indicators/weather-climate EPA. Climate Change Indicators: Heat Waves. https://www.epa.gov/climate-indicators/climate-change-indicators-heat-waves Harvard Health Publishing. What is a plant-based diet and why should you try it? https://www.health.harvard.edu/blog/what-is-a-plant-based-diet-and-why-should-you-try-it-2018092614760 Healthline. Cycling vs. Walking: Which Is the Better Workout for You? https://www.healthline.com/health/fitness/cycling-vs-walking#bottom-line NASA. Examining the Viability of Planting Trees to Help Mitigate Climate Change. https://climate.nasa.gov/news/2927/examining-the-viability-of-planting-trees-to-help-mitigate-climate-change/ Pew Research. As Economic Concerns Recede, Environmental Protection Rises on the Public’s Policy Agenda. https://www.pewresearch.org/politics/2020/02/13/as-economic-concerns-recede-environmental-protection-rises-on-the-publics-policy-agenda/ The Washington Post. Six steps the world can take to halt climate change. https://www.washingtonpost.com/climate-solutions/2022/04/04/ipcc-climate-change-solutions/ Reuters. World’s Top Banks Pumped $742 Bln into Fossil Fuels in 2021 – Report. https://www.reuters.com/business/sustainable-business/worlds-top-banks-pumped-742-bln-into-fossil-fuels-2021-report-2022-03-30/Make Change Staff
September 2, 2022
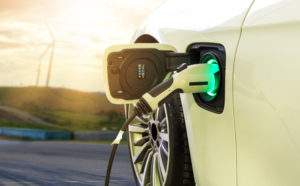
6 Sustainable Innovations Creating a Greener Future
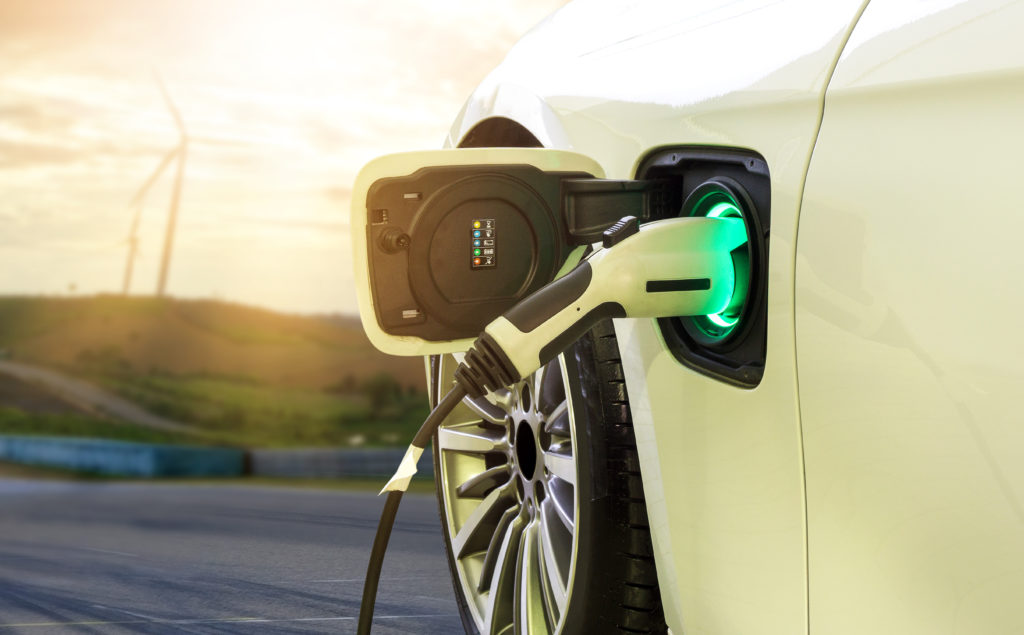
#1 Electric Vehicles
Since 1890, electric vehicles have captured the minds of socially-conscious societies. But it’s only recently that electric vehicles have captured the world’s hearts. That’s because, for the first time since the combustible engine, automakers are realizing electric vehicles’ potential for profit and positive climate action. The reason? Dramatically reduced carbon emissions. A traditional gas-guzzler emits 11,435 pounds of CO2 per year, while an all-electric vehicle contributes 3,932 pounds of CO2 (the vehicle itself emits zero pounds, but the power plant that produces the electricity emits carbon). As a result, an increasing number of cities—from New York to Shenzhen—are mandating the switch to electric vehicles. The disruptive innovation of the electric vehicle is changing our automotive future in three key areas:- Personal transport – All-electric, plug-in hybrid, and hybrid electric vehicles are becoming more widespread. In 2021, over 6.6 million electric cars were sold, and this number is expected to rise every year. Soon, highways may be full of carbon-friendly sparks—not carbon-heavy emissions.
- Public transport – To reduce carbon and other greenhouse gas emissions, many major cities are adopting sustainable practices like electric public transport vehicles. In China, for instance, eBuses dominate public transportation, and many European cities are expected to follow suit.
- Private trucking – The days of gas-guzzling big rigs barreling down the interstate may soon be over. Instead, shipping lanes may soon be dominated by eTrucks. In fact, some pundits predict that by 2030, battery-electric commercial vehicles may surpass traditional EV sales.
#2 Plastic Recycling Technology
From grocery bags to automotive parts, plastic materials dominate many societies. While plastic does offer affordability and convenience (plastic spork, anyone?) it also contributes to climate change in two important ways:- Plastic manufacturing – Manufacturing plastics involves burning a ton of fossil fuels, primarily petroleum. In fact, petroleum is so central to plastic manufacturing that some scientists speculate that if we don’t reduce plastic consumption, 20% of oil production will go towards plastics manufacturing by 2050.
- Plastic recycling – Although blue recycling bins are mainstays in most modern households, the truth is most plastic doesn’t get recycled. Instead, most recycled plastic gets dumped into landfills. Even worse? A sizable percentage of plastic waste makes its way into lakes and oceans, where it releases greenhouse gas emissions as it breaks down. This waste also poses a significant danger to marine life.
- Plastic-eating bacteria – Some bacteria species are known to munch on non-biodegradable plastics and turn them into biodegradable polyester. Scientists are working to genetically modify these bacteria so that they become even better plastic-munching powerhouses.
- Turning plastics back into oil – If plastic is derived from petroleum, why can’t it also be broken back down into petroleum? That’s what scientists are asking while designing depolymerization technologies that can potentially transform plastics into biodegradable materials.
- Getting smart with “smart” polymers – Some companies are experimenting with replacing non-biodegradable polymers with smart polymers as a way to facilitate biodegradability. That way, households and corporations can more easily recycle plastics.
#3 Green Financial Products
When it comes to innovations creating a greener future, green financial products are often an afterthought. After all, reducing plastic use seems a smidge more doable in your day-to-day than advocating for financial products that can help address your carbon footprint. But without eco-friendly financial practices, many companies and governments won’t fund green initiatives in the first place. What’s more, failing to implement green financial practices further empowers the big banks that fund the vast majority of fossil fuel extraction. In short, if money talks, no voice should be louder than clean, green money. Here’s how innovative and sustainable financial services are making it easy to make a big environmental difference:- Green home loans – Many mortgages and government-backed loans incentivize clean energy by offering lower interest rates for homes that meet certain energy-efficient criteria. Additionally, many financial institutions offer commercial builders discounted loans for projects that involve green leadership and solar technologies.
- Green debit and credit accounts – More and more credit card companies are reimagining what it means to “spend & save.” That’s because these green financial companies are linking purchases to positive climate initiatives. In addition, many green credit card companies offer green financial products such as global carbon offsets, discounts and cash back for environmentally-friendly purchases, and green manufacturing of the card itself.
- Green investments – From funding reforestation projects to selling bonds for clean-energy projects, green investments are innovative financial products that can help counter the funding of fossil fuel initiatives.
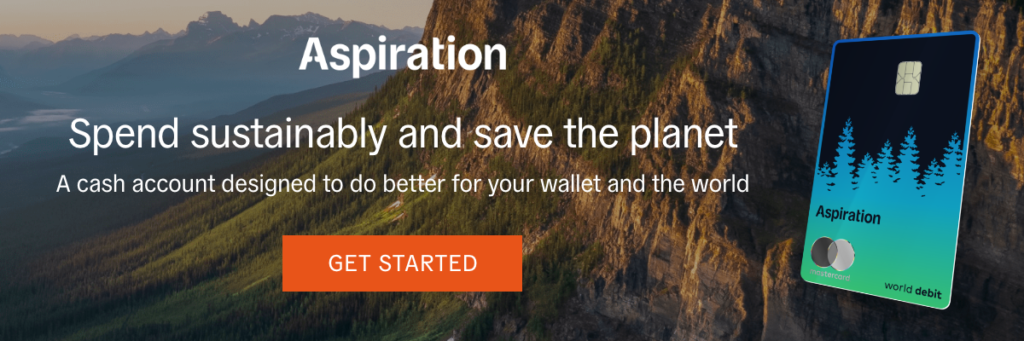
#4 Solar Energy
While we can produce electricity from several resources, the most common source is our natural resource of coal. This means that most electrical production negatively impacts the environment. A possible sustainable solution? Harnessing the power of the sun. Although we’ve known about solar power since the discovery of the photovoltaic effect in the mid-1800s, solar power is slowly gaining traction in the 21st century. In fact, solar power still comprises less than 1% of U.S. electrical generation. But that may soon change. Solar power shouldn’t be discounted when it comes to sustainability innovation. Solar power can help usher in a greener future in the following ways:- Energy from the sun is inexhaustible – As the classic song goes, “The sun will come out, tomorrow…” And the next day, and the next day, and—we think you can get where we’re heading with this. The sun is a resource that will keep on giving for a long, long time.
- Reduces carbon emissions – Unlike coal mining and oil production, solar power produces very little carbon emissions. In fact, the photovoltaic process emits no carbon; the only carbon emitted is during the solar panel construction process.
- Provides electricity to impoverished areas – Much of the world, especially sub-Saharan Africa and parts of the Caribbean, lacks access to electricity. As a result, many companies are expanding their electrical grids into these areas. While access to electricity is ultimately a good thing, these companies use grids that run off fossil fuels. However, in recent years, many companies have subsidized solar power projects in these areas as a part of their sustainable business strategy. These projects provide much-needed power while helping to tackle our carbon footprint.
#5 Carbon-Capturing Technology
Rather than eliminating carbon emissions by reducing the use of carbon products altogether, some innovative technologies are becoming better at capturing carbon after it’s emitted into the environment. The green innovation of carbon-capturing technologies, while still relatively young, are showing big results. Studies suggest that carbon-capturing technologies can trap 90% of carbon emissions. At present, carbon-capturing technologies take three primary forms:- Post-combustion – Post-combustion carbon capture refers to the method where CO2 is separated and captured from the flue gas, which is a byproduct of coal combustion.
- Pre-combustion – Pre-combustion carbon capture involves separating and capturing CO2 before the combustion process is complete.
- Oxyfuel – While not technically a carbon capture technology, oxyfuel has been used to separate CO2 from the combustion process. It works by introducing pure oxygen into the combustion process.
#6 LED Lights
Light-emitting diode (LED) lights have become immensely popular over the past decade—and for good reason. When it comes to how to shop sustainably, these are a great choice for lighting in your home. While incandescent bulbs last, on average, for 1,200 hours while consuming 60 watts of electricity, LED lights are the king of energy efficiency, lasting a whopping 50,000 hours on six to eight watts. As a result, LED lights can seriously help neutralize our carbon footprint. By some estimates, 75% of light bulbs worldwide will use LED technology by 2030, leading to a 1,800 million metric ton reduction in carbon emissions. Finally, an LED light bulb is a sustainable product that emits far less heat than the traditional light bulb, contributing to reduced household energy cooling costs. Talk about sustainable living.Aspire to a Greener Future with Aspiration
From electric cars to carbon-capturing technology, sustainable technology is making our future cleaner, greener, and brighter than we ever thought possible. But why wait for the future when you could change the world today—and receive cash back? Aspiration makes it possible to do your part by purchasing the socially-conscious goods and services you love. All you need to do is sign-up and start taking down fossil fuels one swipe at a time. Welcome to Aspiration, where spending makes a difference. Sources: Electrek. Global market share of electric cars more than doubled in 2021 as the EV revolution gains steam. https://electrek.co/2022/02/02/global-market-share-of-electric-cars-more-than-doubled-2021. Energy. The History of the Electric Car. https://www.energy.gov/articles/history-electric-car. Ennomotive. 5 Innovations In Plastic Recycling You May Not Know About. https://www.ennomotive.com/innovations-plastic-recycling/ Institute for Energy Research. History of Solar Power. https://www.instituteforenergyresearch.org/renewable/solar/history-of-solar-power/ McKinsey Sustainability. These 9 technological innovations will shape the sustainability agenda in 2019. https://www.mckinsey.com/business-functions/sustainability/our-insights/sustainability-blog/these-9-technological-innovations-will-shape-the-sustainability-agenda-in-2019 Means & Matters. Who Funds the FIGHT Against CLIMATE CHANGE? https://meansandmatters.bankofthewest.com/article/sustainable-living/taking-action/who-funds-the-fight-against-climate-change/ MULTIBRIEFS. The environmental benefits of LED lighting. https://exclusive.multibriefs.com/content/the-environmental-benefits-of-led-lighting/facilities-grounds. The International Council on Clean Transportation. Electric vehicle capitals of the world: What markets are leading the transition to electric? https://theicct.org/sites/default/files/publications/World-EV-capitals_ICCT-Briefing_08112017_vF.pdf The London School of Economics and Political Science. What is carbon capture and storage and what role can it play in tackling climate change? https://www.lse.ac.uk/granthaminstitute/explainers/what-is-carbon-capture-and-storage-and-what-role-can-it-play-in-tackling-climate-change/ United Nations Environmental Programme. Green Financial Products and Services Current Trends and Future Opportunities in North America. https://www.unepfi.org/fileadmin/documents/greenprods_01.pdf U.S. Department of Energy. Emissions from Electric Vehicles. https://afdc.energy.gov/vehicles/electric_emissions.html World Economic Forum. We know plastic pollution is bad – but how exactly is it linked to climate change? https://www.weforum.org/agenda/2022/01/plastic-pollution-climate-change-solution/.Make Change Staff
August 11, 2022
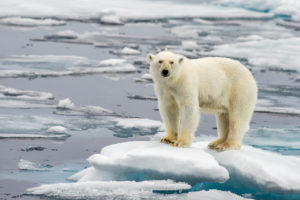
How Much Money is Actually Needed to Solve Climate Change?
From investing in innovative technologies to spearheading new initiatives, solving climate change requires a multifaceted, global approach. Above all our individual, daily efforts, this approach ultimately comes down to money.
So, can we put a price on the health of our planet? How much money is needed to solve climate change? It helps to grasp how much money is spent on climate change mitigation currently—and how much more might be needed to advance our efforts to make a meaningful difference.
We’ll answer those questions and more by doing a financial deep-dive into current climate change policies. We’ll also detail what you can do to help sustain a cleaner, greener planet.
The Current State of Climate Change Spending
To solve climate change, we need more than just the change in our pockets. That’s why it’s elemental to understand the costs on a worldwide scale.
To understand how much we currently spend to counter climate change (sometimes known as climate finance), let’s break down the costs based on spending in the United States and across the globe.
Worldwide Contributions
Between 2019 and 2020, the world spent $632 billion on global warming and climate change mitigation investments and initiatives.
While this sounds like a lot of cash, it’s only a fraction of the estimated $90 trillion we need to spend by 2030, according to World Bank data from October 2019.
Here’s a breakdown of where that $632 billion came from:
- The public sector – Global governments and institutions have been the primary sources of climate change mitigation funding since the enactment of the 2015 Paris Agreement. During the 2019–2020 fiscal year, the global public sector contributed $321 billion to righting the climate change ship.
- The private sector – In recent years, corporations have pledged more resources to help bolster global climate change initiatives. That said, the global private sector’s contribution of $124 billion from 2019–2020 was lower than its 2018 contribution of $183 billion.
- Banking institutions – From 2019–2020, international banks provided $121 billion in loans to jumpstart renewable energy initiatives. However, large banks have also contributed mightily to continued fossil fuel extraction—$1 trillion, to be exact.
- Global funds – Private investment funds such as venture capital and private equity hedge funds contributed $8 billion from 2019–2020.
- Individual households – Worldwide, individual households contributed $55 billion from 2019–2020.
While $90 trillion is certainly a significant investment, the World Bank says these investments to combat climate change can be recouped, with a climate investment of $1 yielding, on average, $4 in benefits.
The United States’ Contribution to Climate Change Spend
Now, let’s take a look at U.S. spending on the climate crisis.
Tracking the United States’ contribution to fighting climate change can be a monumental task—not in the least because climate change funding varies greatly depending on the current administration.
That said, according to the Office of Management and Budget, the U.S. spent $13.2 billion across several agencies in 2017. In addition, the United States government has spent close to $154 billion on climate-related activities since 1993.
The government has funneled the bulk of this funding into three climate change-related categories:
- Technology
- Science
- International assistance
While U.S. climate change spending lagged during previous administrations, it’s clear that climate-minded administrations can make a difference. For instance, the Biden administration pledged $555 billion in 2021 for programs to fight climate change.
The Human Impact on the Climate
Another facet of determining how much money is needed to stop (at this point, mitigate) climate change is to understand our current impact on the planet’s health—and how we can do better.
In general, we can measure our impact on the climate across several metrics, including:
- Carbon dioxide levels – Since 1958, carbon dioxide levels have risen by 25%. Since the Industrial Revolution, carbon emissions have risen by 40%. The primary reason for this rise is our continued use of fossil fuels.
- Global temperatures – Global temperature fluctuations occur naturally over millions of years. However, sharp increases (or decreases) over a relatively short period of time indicate negative climate change. From 1901 to 2020, the Earth’s temperature increased by 1.8 degrees Fahrenheit.
- Glaciers and sea ice – By looking at glacier melt and sea ice change, climate scientists can paint a clearer picture of the negative climate impacts. According to NOAA, 30 well-studied glaciers have shrunk by an average of 60 feet since 1980. Additionally, Arctic sea ice has shrunk by 40% since 1979.
- Rising sea levels – When glaciers and sea ice melt, global ocean levels tend to rise. Since 1993, the sea has risen by 3.2 mm/year.
In addition to the above metrics, scientists are paying attention to the increase in frequency, duration, and severity of natural disasters. An increase in natural disasters reflects continued negative climate change.
The Importance of Investing in Climate Change Action
Reversing the damages brought on by climate change will require significant collective efforts, but it’s not impossible. It’s going to take a concerted global endeavor—and a lot of money. To be exact, $4.31 trillion of it.
But how can money help climate change?
For some scientists and economists, climate action starts with funding clean energy infrastructures that reduce greenhouse gas emissions. For both individuals and institutions, it also means switching from big banks that finance the fossil fuel industry to more sustainable financial services.
Individuals can also invest in climate change initiatives in the following ways:
- Reduce plastic consumption
- Reduce food waste
- Switch to electric cars and other carbon-neutral transportation
- Commit to clean money
- Support carbon capture projects
- Learn how to invest in carbon credits
By investing in climate change action on the individual, corporate, and governmental levels, we aren’t just funding climate change initiatives today. We’re writing a check for a better tomorrow.
Changing the Planet One Swipe at a Time
Let’s face it: we can’t solve global warming and climate change alone. It will take a concerted effort from governments, corporations, and, most importantly, people like you.
Fortunately, Aspiration gives new meaning to the phrase “spend & save.” That’s because Aspiration lets you plant a tree every time you swipe your green credit card or eco-friendly debit card. Planting trees remains one of the most impactful ways of reducing the effects of climate change through the capture of carbon emissions.
You can also rest easy knowing your deposits will never fund fossil fuel industry projects. Talk about clean money.
Get started with Aspiration today and positively change the planet one purchase at a time.
Sources:
FiveThirtyEight. How Much Is The Government Spending On Climate Change? We Don’t Know, And Neither Do They. https://fivethirtyeight.com/features/how-much-is-the-government-spending-on-climate-change-we-dont-know-and-neither-do-they/
Means & Matters. Who Funds the FIGHT Against CLIMATE CHANGE? https://meansandmatters.bankofthewest.com/article/sustainable-living/taking-action/who-funds-the-fight-against-climate-change/
National Oceanic and Atmospheric Administration. Climate change impacts. https://www.noaa.gov/education/resource-collections/climate/climate-change-impacts
The New York Times. House Passes the Largest Expenditure on Climate in U.S. History. https://www.nytimes.com/2021/11/19/climate/climate-change-bill.html
U.S. Government Accountability Office. Climate Change: Analysis of Reported Federal Funding. https://www.gao.gov/products/gao-18-223
Yale Insights. Why We Need Finance to Fight Climate Change. https://insights.som.yale.edu/insights/why-we-need-finance-to-fight-climate-change
The United Nations. Financing Climate Action. https://www.un.org/en/climatechange/raising-ambition/climate-finance
Make Change Staff
August 10, 2022
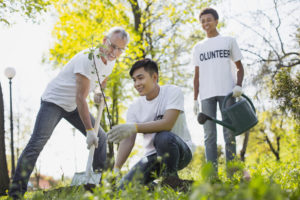
11 Best Environmental Charities to Donate To

#1 Crypto Climate Accord
The Crypto Climate Accord is a forward-thinking, decarbonization-focused organization fighting to make the cryptocurrency industry climate-neutral in record time. Primarily, it seeks to give crypto stakeholders the tools they need to provide crypto miners, exchange platforms, and investors the means to:- Calculate the energy use and greenhouse gas impacts of various cryptocurrencies
- Digitize renewables and carbon offset exchanges
- Provide and seek proof of green operations verification
#2 Planet Impact Fund
The organization 1% For The Planet has created avenues for sustainable investment since 2002. Their Planet Impact Fund serves two crucial purposes:- Resourcing nonprofit organizations working to address the most urgent environmental issues
- Powering investments in a sustainable, healthy world
- Climate action
- Environmental justice
- Conservation efforts
- Clean energy technologies, advancement, and innovation
#3 1t.org
Among all the climate change charities listed here, 1t.org embodies the roots of the environmentalist movement: its mission is to conserve, restore, and plant trees worldwide. To accomplish this, they focus on three efforts:- Mobilizing the private sector to monetarily and social invest in climate action
- Facilitating partnerships between workers, organizations, and world governments
- Supporting green innovators and entrepreneurs in developing their sustainable systems to scale
#4 Project Drawdown
Project Drawdown is a world leader in climate-focused sustainable innovation, knowledge, and action strategies. It builds evidence-based resources to help governments, individuals, and other entities reach the drawdown—the threshold when emissions begin to decline instead of steadily increasing. The organization provides climate action implementation resources for numerous sectors, including:- Electricity and energy
- Food, agriculture, and land use
- Transportation
- Industry and manufacturing
- Buildings and construction
- Education
- Habitat and resource sinks such as:
- Land sinks
- Coastal and ocean sinks
- Engineered sinks
#5 Founders Pledge
Founders Pledge is an environmentalist organization connecting climate innovators and sustainable entrepreneurs with four essential resources:- Funding
- Investment infrastructure
- A network of climate professionals with whom to consult
- Evidence-based environmental knowledge and data
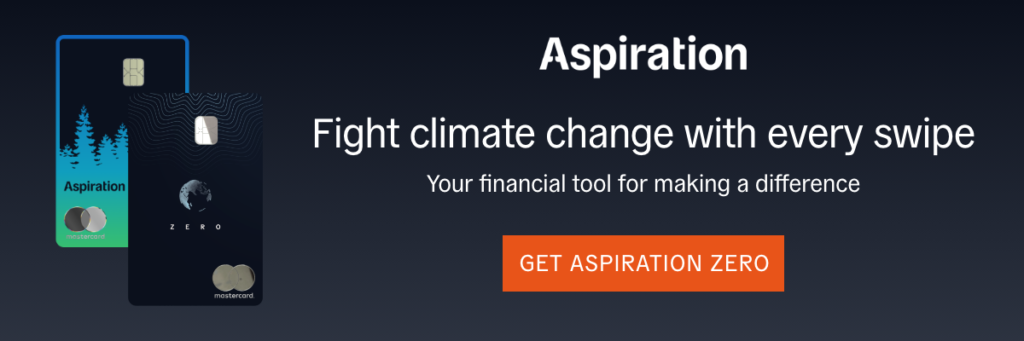
#6 Cool Earth
Cool Earth is a nonprofit organization leveraging one of the most important resources we have to fight climate change: Indigenous peoples’ intimate, firsthand knowledge of land stewardship, nature conservancy, and environmental protection. As one of the numerous green charities empowering Indigenous communities worldwide, Cool Earth seeks to plant and protect trees, initiate projects that help Indigenous peoples protect their homelands, and capture carbon. So far, the organization has:- Planted over 100 million trees
- Powered 40 Indigenous-centered projects
- Stored 117 million tons of carbon emissions
#7 Indigenous Land Trusts
Like Cool Earth, Indigenous land trust organizations understand and seek to promote the centuries-long cultural connection between Indigenous peoples and their land stewardship methods. Numerous types of land trust organizations exist, and they fall into one of two categories:- Entities that support specific tribes
- Organizations that connect tribes with resources, information, and financial support
- Reinvigoration of Indigenous culture within Native communities
- Restoration of traditional ecological knowledge and land protection practices
- Recovery resources for intergenerational trauma, which can adversely impact land stewardship capabilities
#8 Ocean Conservancy
Ocean Conservancy is one of the most well-known charities for environmental action. They support marine conservation, advocacy, and education, fighting the biggest threats to the world’s oceans through evidence-based, science-endorsed solutions. As a broad-scale organization with a long track record for building conservation solutions at scale, Ocean Conservancy steers financial resources, professional expertise, and its devoted cadre of volunteers toward seven major projects:- Confronting Climate Change
- Government Relations
- Protecting Florida
- Protecting the Arctic
- Smart Ocean Planning
- Sustainable Fisheries
- Trash Free Seas
#9 Environmental Law Alliance Worldwide
Environmental Law Alliance Worldwide or ELAW is a collective of attorneys, climate advocates, and scientists. Their mission is to empower everyday people and world leaders alike with the empirical evidence they need to advocate for environmentalist policies in a legal setting. ELAW was founded in 1989 in North America by a team of lawyers representing ten different countries around the globe. Using a combination of strategic counsel, legal support, and scientific information, they pressure decision-makers to push forward climate-progressive policies in their home countries and beyond. Today, donations made to ELAW are used to:- Connect attorneys, environmental advocates, and scientists who are working to ensure climate policies accord with sustainability goals
- Provide legal resources to organizations devoted to environmental justice and stewardship
- Subsidize educational initiatives like research fellowships, webinars, and online panels
- Ensure environmental advocates and lawyers are protected while pursuing policy change through legal action
#10 Community Forests International
Community Forests International works to connect sustainability initiatives in three forest ecosystems in geographically disparate states: Canada, Mozambique, and Zanzibar. This organization is dedicated to pursuing “natural climate solutions.” Experts and advocates from each nation share three main goals:- Restore and protect regional forests and wildlife
- Help communities adapt and adjust to the impacts of climate change and global warming
- Develop local economies centered around sustainable problem-solving
#11 Clean Air Task Force
Named one of the most cost-effective environmental organizations by Founders Pledge, the Clean Air Task Force has one mission: to reduce air pollution by decarbonizing global energy systems by 2050. The CATF is governed by a summit of scientists, engineers, lawyers, business, and policy experts. Together, they’re focused on reducing impact in four key sectors:- Electricity
- Transportation
- Industry
- Infrastructure
Aspiration: Integrating Climate Action and Money Management
This list of the best charities for environmental impact represents a community of organizations far and wide, large and small, and young and old, who are working in tandem towards a cleaner, greener future. As part of our mission, Aspiration is proud to support several organizations above. We do our own to support each facet of climate progress, from helping members offset their carbon emissions at the gas pump to managing sustainable investment portfolios. Whatever cause you want to put your dollar towards, we’re here to help you navigate the complexities of eco-friendly personal finance. To learn more about what a climate-forward approach to managing your money looks like, explore Aspiration’s sustainable financial services today. From an eco-friendly debit card to a sustainable investment fund, we make it easy for you to put your money where your values are. Sources: Crypto Climate Accord. POWERING CRYPTO WITH 100% RENEWABLES. https://cryptoclimate.org/solutions/ 1% For The Planet. Planet Impact Fund. https://onepercentfortheplanet.org/planet-impact-fund?hsLang=en 1t.org. Our mission. https://www.1t.org/about-us Project Drawdown. Programs. https://drawdown.org/programs Founders Pledge. Our Approach. https://founderspledge.com/high-impact-giving Cool Earth. Act Now. https://www.coolearth.org/act-now/ Amah Mutsun Land Trust. The Native Stewardship Corps. https://www.amahmutsunlandtrust.org/native-stewardship-corps Ocean Conservancy. Programs. https://oceanconservancy.org/programs/ Environmental Law Alliance Worldwide. Mission and History. https://elaw.org/about Community Forests International. What We Do. https://forestsinternational.org/homepage/about/what-we-do/ Founders Pledge. Climate Change Cause Area Report. https://founderspledge.com/research/fp-climate-change Clean Air Task Force. Join Us. catf.us/join/Make Change Staff
August 9, 2022
Follow Us on Instagram to Plant One Tree
Join our Community
Green Finance
Discover why it matters to put your money where your values are.